World-leading aircraft component manufacturer, Globe Engineering, has installed a fourth Unison all-electric CNC tube bending machine at its facility in Wichita, Kansas.
Commissioned earlier this year, the new machine has joined Globe’s existing Unison all-electric tube benders at the Wichita site and will help to increase manufacturing capability significantly. With overlapping capacities, the Unison tube bending machines at Globe can bend tubes from 1.25” (31.75mm) to 6.00” (152.4mm) in diameter – all with the highest levels of repeatability and accuracy.
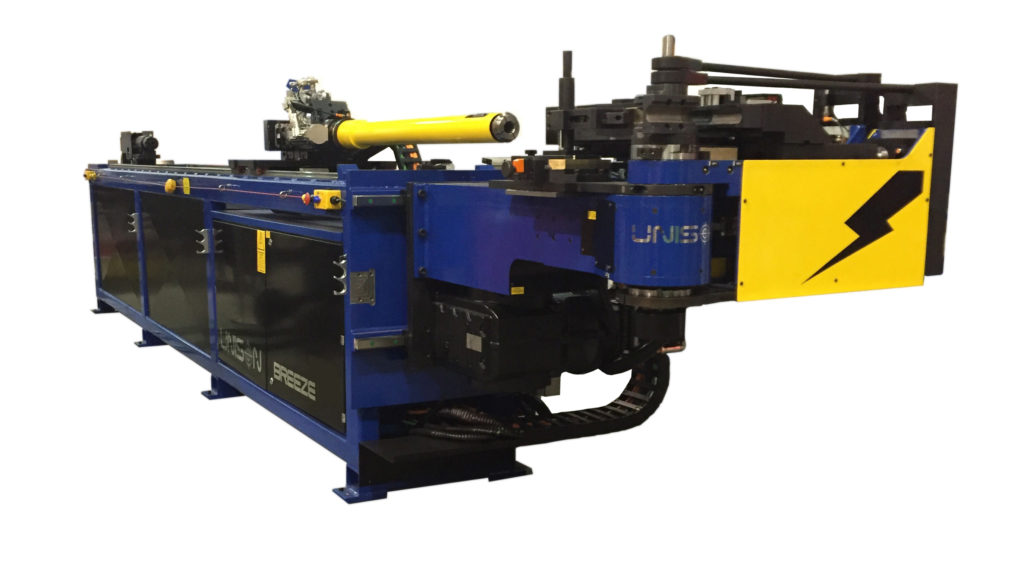
In addition to supporting Globe’s ongoing requirements for bending high quality aircraft tubing, the new all-electric CNC tube bender from Unison will be used to bend a range of aluminium, stainless steel and titanium tubes measuring up to 1.25” (31.75mm) in diameter. Before investing in this latest machine from UK-based Unison, Globe had just one tube bending machine that was capable of bending stainless and titanium tubes from 5/8” to 1.00” diameter.
“We aren’t just creating new capability by buying a new Unison tube bending machine,” explains Bend Shop Supervisor Shaun Knuth. “We’re creating capacity and a safety net, in case we have a breakdown.”
Describing some of the key advantages that Unison all-electric tube benders have over hydraulic tube benders, he adds: “They’re more efficient because they use less energy. In fact, they only use energy while they are in motion. By comparison, the hydraulic benders use electricity all the time they are running, with their energy usage increasing during cycle time. Electric machines are much quieter too. Our Unison all-electric tube benders also offer greater repeatability. You simply select the exact pressure you need; if you want 1,272 psi of pressure, you just type that in, and the machine creates exactly the same pressure every time.”
Shaun Knuth also praises the fact that Unison all-electric tube benders can be operated more slowly when hot-bending titanium, all the way down to a creep – a process that removes the risk of overheating and minimises scrap. He also points out that there’s no need for titanium tubes to be lubricated with expensive, messy grease before hot bending when using all-electric machines.
“Unison machines are built like tanks”
“Unison machines are built like tanks,” adds Shaun Knuth. “And if there’s a problem, we usually have a new part within a few days. The machines are so easy to use and we can install the parts ourselves. Additionally, Unison technicians can remotely check our repairs, and upgrade each machine’s software and firmware.”
Steve Haddrell, Key Account Manager at Unison, adds that Globe Engineering’s latest order is particularly rewarding for several reasons. “Repeat orders are always great news because they carry a clear customer endorsement. Globe Engineering relies heavily on its tube bending machines and is familiar with the benefits of Unison’s all-electric technology, including fully automated machine set-up, ease of use, very high bend accuracy and excellent repeatability.
“In this case, the company decided that these attributes, combined with the build quality and reliability of Unison machines, significantly outweighed any short term economic advantage of low cost tube benders. Increasingly, our customers regard Unison as a solutions partner, with our machines forming part of their long-term business strategy.”
About Globe Engineering
Globe Engineering has been innovating aerospace manufacturing solutions since Albert Nelson Jr. founded the company in 1946. Based in Wichita, Kansas, Globe serve the likes of GE Aerospace, Bombardier, GKN & Marshall. For over 70 years, Globe Engineering has built quality aircraft components and assemblies for the commercial, defence and general aviation industries. Globe performs many different processes under one roof, helping to improve efficiency and ensure quality. From the very beginning, Globe employees have earned an unmatched reputation for tackling tough jobs, with outstanding quality and on-time delivery.
About Unison Ltd
Established in 1973, Unison Ltd is the UK’s leading manufacturer of tube and pipe bending machines, with the largest range of all-electric tube benders from 5/8” (16mm) to 10” (273mm) in diameter. Unison Ltd has continued to innovate the tube and pipe bending marketplace, from manufacturing the world’s first all-electric tube bender in 1994 and the world’s first all-electric multi-stack tube bender, to building the world’s largest tube bender for Westcon Yard AS, who operate one of the most modern and successful shipyards in the industry.
Unison’s tube bending software is recognised as the most user-friendly control system for tube bending machines. The software is written and supported by Unison, ensuring complete control of its evolution and no need for third party support.
Source: WIRE AND TUBE NEWS