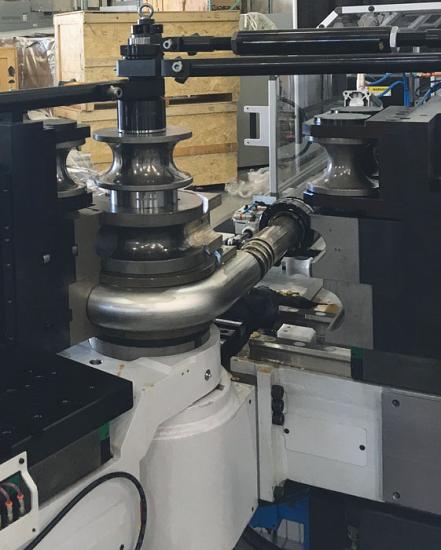
Stainless steel has been around for a long time, and it is nothing new for tube applications. The lure, luster, and longevity of stainless beg for its use in tube and pipe, and it’s not just used in the exotic or aircraft markets anymore. High-end stainless grades have made their way into more mainstream and high-volume applications and, as bend radii decrease and the desire for downstream process compatibility increases, the challenges compound. Selecting the right lubricant for your tube bending process can help you navigate the variables and contribute to process efficiency, consistency, and success.
A More Stainless World
While scores of stainless grades are available, alloy 304 accounts for nearly 50 percent of all stainless steel produced, which is followed by 316 (marine grade) and 409, a ferritic alloy used heavily in the automotive market. Alloys in the 300 series—austenitic, high-nickel grades—are making their way into high-volume applications such as automotive exhaust systems for appearance, strength, and corrosion resistance. Meanwhile, some ferritic grades such as 439 also are becoming more widely used for their strength, as well as heat and corrosion resistance.
Replacing a carbon steel with a stainless alloy comes with tradeoffs, one of which is bending difficulty. Much of this is due to the increased strength and hardness. The topography of stainless steels plays a role as well. The surface is much smoother than carbon steel, leaving fewer and smaller pockets for lubricant to reside in during the bending process. Less lubricant and more substrate-to-tool surface contact usually translates to more heat, friction, and perhaps rips or tears. Because of these attributes, better-performing lubricants with good barrier and extreme-pressure (EP) protection, and in some cases smaller molecule sizes, can help to overcome the challenges associated with bending stainless steel tubing.
D of Bend and Other Variables
Higher stainless grades can be more challenging with respect to material properties, but they can be bent successfully. In some cases, the product designer can engineer the part to have a longer centerline radius (CLR) to reduce the bending severity. When a tight radius is necessary, the process gets exponentially more difficult, requiring more performance from the lubricant.
Meanwhile, many high-volume suppliers desire to take any excess material out of the equation to save on process costs. This results in a minimum wall thickness (t). If the tube’s outside diameter (OD) remains constant, the wall factor (OD/t) increases, making the bend more challenging as the material along the outside of the bend elongates and the material along the inside compresses (see Figure 1).
jLikewise, the D of bend (CLR/OD) is a key factor. As the D of bend decreases, the bend becomes more challenging to achieve successfully. When the D of bend decreases to less than 1.25, better lubrication is increasingly necessary to carry the increased frictional load. Likewise, as the wall factor increases, so does the severity and need for better lubrication. Both variables, along with bend angles and surface finish, help to determine the best lubricant for stainless steel bending.
Focusing on the Entire Process
When it comes to bending high-end stainless materials, most of the attention is on the increased difficulty in bending. This leads to changes upfront in tool and lubricant selection. However, those changes then lead to deviations downstream in secondary processes like welding and cleaning.
The focus starts with the right tool set. Using the optimal tool material and setup is the largest influence on successful bending. A bronze material normally is used for the mandrel and wiper dies when bending regular stainless steel, but the increased hardness of higher-end stainless adds more difficulty and more tool wear (see Figure 2). Hence, many suppliers and users are looking at tool coatings to help bridge the gap and decrease wear.
This tactic has been successful with topical and light thermal-diffusion coatings. However, some of these coating processes cause the bronze material to become too brittle to use, and therein lies the conundrum. Softer tooling material is needed to bend the harder substrate, but softer materials wear more quickly; increasing the hardness with a coating nullifies the advantage of using a softer material. Tool suppliers can recommend the best options available, but if physics leads to too many unresolved questions, chemistry may hold the answers.
A heavier-duty lubricant certainly will lead to process changes. First is lubricant application. Getting the lube to the wear points is crucial and when several bends are made on one tube, the lube often just does not carry through. Lubricant application specialists can help to determine the best method to get the lube from the container to the bending process.
Lubricant removal might be necessary, and remaining residues might have to be washed off the tube. Trying to weld through the residue can be difficult or impossible and can lead to substandard, porous welds.
Time for a Regime Change
This leads to the big question: Which is the best lubricant for bending high-end stainless steels? There is no clear-cut choice, but evaluating each process step and taking into account every process requirement helps to narrow down the options. Of course, the lubricant that works best in one situation might not work the best in another situation, even when the process variables seem identical.
The most common and adaptable products for high-end stainless steels are straight oils of light to medium viscosity. These can be petroleum- or vegetable-based oils containing barrier and EP additives. In addition, chlorinated paraffins perform very well because they provide a good barrier film as well as a supplementary chemical barrier, which is activated by the extreme heat and pressure generated by bending.
Viscosity can help carry some of the load, but it has to be just right. A lubricant that is too thick can cause some drag and application issues; if it’s too thin, it will not stay on the circumference of the mandrel, leaving it susceptible to dry spots.
Furthermore, the application method is critical. Getting the lubricant into the pores is necessary. Straight oils are used as is (without water dilution), so after the bend is complete, removal may be necessary before secondary processing. Polymers and other EP additives have made inroads to providing the extreme pressure and barrier film protection and allowing for easier cleaning if needed. This typically is done by using a water-soluble product in its neat form and then using its solubility in a wash process to help remove the residue from the tube.
Gels and pastes also do well. Gels typically are free of petroleum oil, whereas pastes have some oil content. The best performers usually are those that contain EP additives.
Viscosity plays the main role, but adding solid film lubricants can help to reduce the coefficient of friction further. For example, in one case of 316 (with a 2.5-inch OD, 0.050-in. wall thickness, 1.25 D degree of bend, 90-degree bend angle, and brass mandrel and wiper die), a medium-viscosity vegetable oil with EP additives outperformed a synthetic gel, a paste, and a straight petroleum by eliminating scoring and tearing. In another case involving 304 (with a 3-in. OD, 0.065-in. wall thickness, a 1.5 D of bend, 15- to 90-degree bend angle, and brass mandrel and wiper die), the tube was making a lot of groaning noise and some chattering on the pipe. In this case, several types of lubricants were tried, including heavy EP gels, medium to heavy chlorinated and sulfurized straight oils, soluble oils, and some combinations of each. In the end, it took a paste with a solid film barrier additive to eliminate the groaning.
Although many of the lubricants available these days are heavy duty, these products can still be implemented with health, safety, and environmental awareness. Some of the products can contain great performance additives and still have no hazardous ingredients.
Source: thefabricator