Seeing an opportunity 14 years ago Matthew Levett and his wife Maria founded ML Fabcuts to provide a sub-contract service for waterjet and flat sheet laser profiling. When the need to relocate to its current premises in Crayford arose in 2015, Matt saw this as an opportunity to review ML Fabcuts’ output with greater emphasis being placed on laser profiling, while retaining some waterjet capability.
Now, two years on from that move the company is tapping in to new potential business with the addition of laser tube processing following a major investment in a BLM LC5 flat-bed laser with integrated tube cutting module.
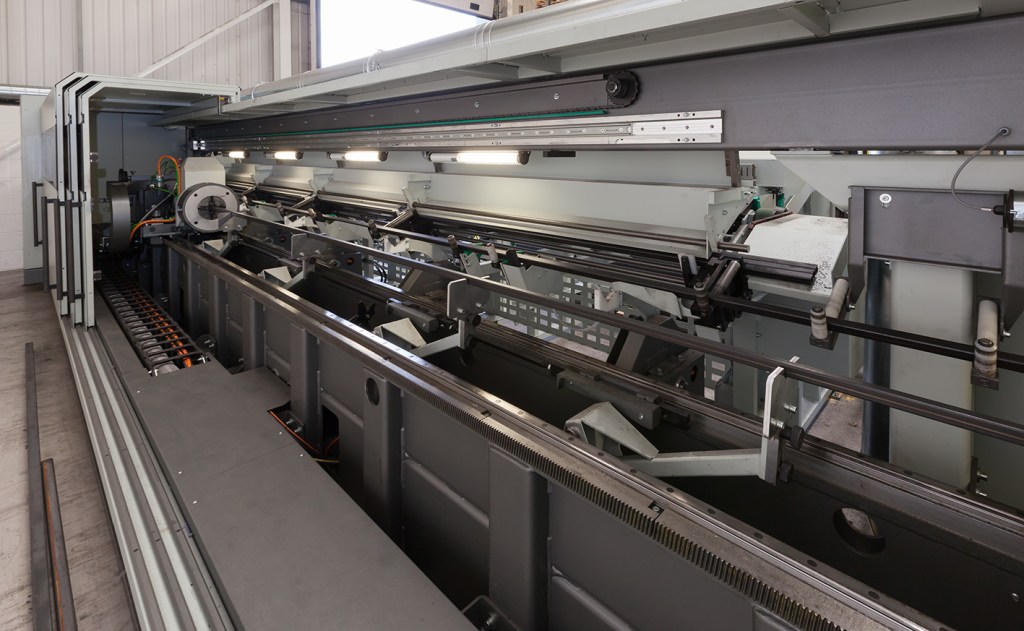
ML Fabcuts built its success and reputation on its rapid response to customers' needs, which it achieved through its willingness to stock sheet in various materials from 0.7 mm thick up to 50 mm thick; alongside the strong team ethic at the family-owned business that makes sure the job gets completed on-time. The result is an extremely diverse customer base ranging from motorsport through the construction industry and signmaking sector to processing one-off commissions for artists. The arrival of the BLM LC5 will further enhance this high level of customer service. "We are all motivated to deliver on our promises, and our list of long-standing customers is testament to the fact we are achieving that," says ML Fabcuts Production Manager, James Waldron-Stevens.
While Matt Levett identified the potential opportunities presented by tube laser cutting, he remained cautious and didn’t want to commit to a dedicated tube laser machine. However, during a visit to the EuroBLECH exhibition, both Matt and James had what they describe as a 'eureka moment' after seeing the 5 kW fiber laser BLM LC5 with integrated tube cutting module. “We had known about BLM and their reputation for tube processing, but when we saw that it was possible to combine tube cutting with flat sheet processing in a seamless package it was almost an instant decision to place an order. The combination of flat bed and tube gave us peace of mind as the machine could still be used as a flat-bed machine if the tube business didn't develop," says James. As it is, with the machine only being installed in May 2017 it is already running at 50/50 tube/sheet capacity with the aim to increase its use on tube processing to 75 per cent.
The efficiency of the BLM LC5 is enhanced by its use of a single laser source and cutting head for both sheet and tube processing, this makes switching from one process to another extremely quick, with ML Fabcuts already making use of this feature to meet customer demands. “We simply push a couple of buttons and we can stop processing sheet, cut some tube, then return to where we left off with the sheet once we have finished the tube work.
It is a feature that I'm sure we will make very good use of to meet urgent deliveries." says James. Automation is central to the design of the LC5 as it comes with automated tube bundle loading capable of handling tube up to 6.5 metres in length and up to 120 mm diameter. Sheet loading is handled by the BLM Electric sheet pallet changer, which can be specified as 3000 x 1500, 4000 x 2000, or 6000 x 2000 mm in size and can be transverse or in-line configuration. ML Fabcuts also took the option of automatic nozzle change, which as well as changing the nozzle, with up to 18 nozzle positions available, it also automatically adjusts it for material and thickness changes, with a vision system monitoring nozzle wear and providing verification that the change has been completed.
Given the size and configuration of the LC5 it comes with two operator panels, one next to the tube processing area, with the second in front of the sheet processing area. "The design and ergonomics of the LC5 just look like it was meant to be and we look at it now as our flagship machine. While we bought it for the tube processing capacity the option of being able to instantly switch to flat sheet means that we have also increased our sheet processing capacity, and it fits our philosophy perfectly adding to our commitment to be a one-stop-shop for customers. " says James. ML Fabcuts has also witnessed an improvement in cut quality from the BLM Fiber laser, due to the additional power that it offers over their existing lasers. This has improved cut capability and virtually eliminated any deburring requirement, particularly when cutting aluminium.
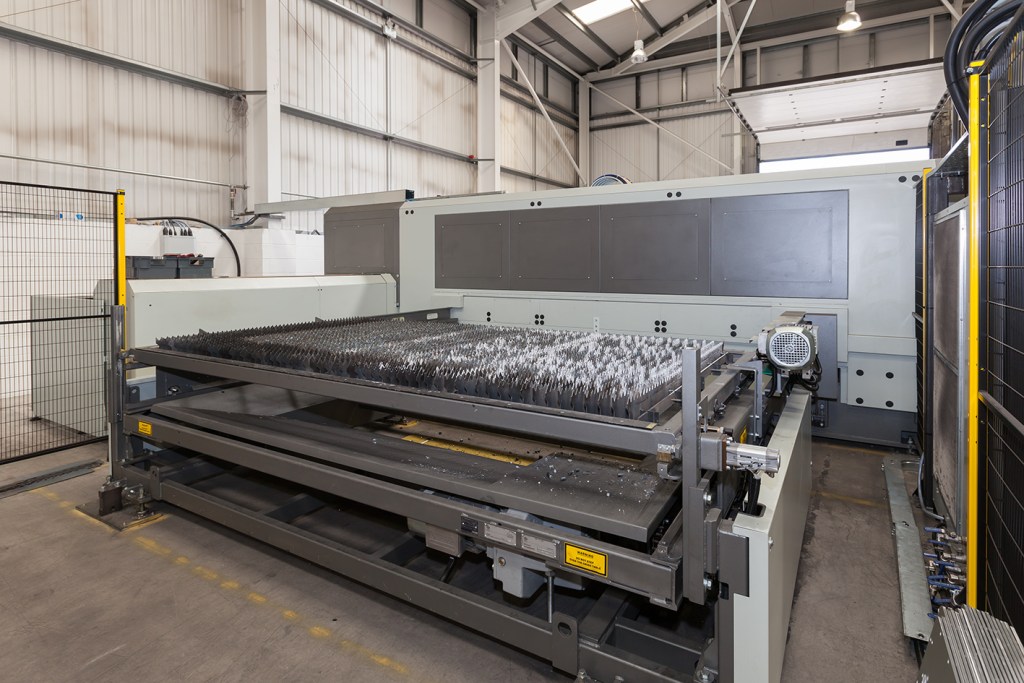
"The entire process from looking at the machine at EuroBLECH to it being installed at our Crayford factory was straightforward. During the initial discussions Jon Curtis at BLM answered all our questions and gave us the confidence that we were ordering exactly what we needed, with no pressure to sign on the dotted line. With the machine installed Matt and experienced estimator Connor Dulson spent a week at BLM in Italy to familiarise themselves with the offline programing software Artube. This initial training was this was followed up with on-site training from BLM at our factory in Crayford for Simon Coe and two other operators as back-up, from there it has all been plain sailing. Our challenge now is to keep it fed with work as its efficiency means that it is a hungry beast, but the reaction we are getting from customers now that we have this combination of tube and flat sheet is very positive," concludes James Waldron-Stevens.
Source: Wire and Tube News