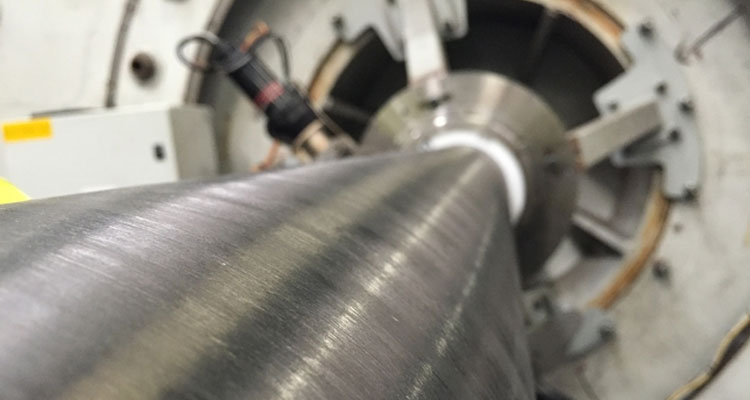
Easily accessible offshore oil deposits are beginning to run out. So to obtain this valuable raw material from new sources, drilling now needs to go much deeper – and this is clearly a technical challenge. Quite often, therefore, fixed oil rigs are accompanied by floating ones. According to Evonik, it means laying flexible pipelines instead of using rigid steel – lines that need to be protected against seawater corrosion on the outside and against oil, gas and water damage from within. "Moreover," says Evonik, "the deeper you go, the more you need to reduce the weight."
Steel and plastic
Pipes which are suitable for this purpose have been unravelled and laid, for instance, some 12 km (7.5 miles) off the Scottish coast, where oil is now being extracted from the seabed via pipelines, using a floating rig.
"The movable pipes have wall thicknesses of at least 6 cm (2.4 inches)," says Evonik. Also, they have at least eight coats, some made from steel and others from VESTAMID® NRG polyamide. While the steel coats mainly serve to provide reinforcement, the plastic layers ensures that the pipes stay tight. "The pipes are resistant to saltwater and also to any of the chemical compounds in the oil." An inner coat of VESTAMID® NRG keeps the oil safely within the pipelines, which can be up to 350 mm (1.4 inches) in thickness. On the outside another plastic layer serves to protect the steel from seawater corrosion. "Pipes with VESTAMID® NRG have been laid not only in the North Sea, but also, for instance, offshore near the Brazilian, West African and Australian coasts."
Pipes are getting lighter
The deeper a company drills, the more it needs to pay attention to the weight of the pipeline. To enable oil extraction at extreme depths, i.e. below 2,500 metres (8,200 feet), Evonik has worked with the Dutch pipe manufacturers Airborne. The result is a lightweight composite pipe which consists entirely of VESTAMID® NRG, reinforced by glass fibre. The Malaysian mineral oil company Petronas, for instance, is planning to use offshore pipes without any steel whatsoever.
The worldwide extraction of oil and gas on the high seas requires innovative and complex pipes made from high-quality materials. This is the trend which Schoeller Werk has followed for a number of years now. It has developed some highly robust control line and chemical injection pipes, made from stainless steel and nickel-based alloys and which can be used at a depth of 10,000 metres (33,000 feet) below sea level. They pump chemicals into the oil reservoir and serve as hydraulic control lines for safety valves. "Thanks to the excellent quality of their surfaces and especially also their welding seams, these pipes can withstand extreme conditions, such as high pressure, temperatures up to 300°C, aggressive media and saltwater," says Markus Zimmermann, head of Energy Sales at Schoeller Werk. "Users benefit from secure installations with above-average lifetimes." In addition, the company’s portfolio for offshore oil customers includes a wide range of services, such as the encapsulation, flushing and filling of pipes.
High-performance materials are in demand
Schoeller Werk has identified a trend whereby the most important requirements on offshore pipes are dimensional stability and corrosion resistance. "So our customers often decide for high-performance materials such as alloys," says Markus Zimmermann.
However, the production and transportation of oil and gas requires not only efficiency, but also safety. Although safety standards are already very high, they still need developing. "As pipe manufacturers, a large part of our steel pipes go to the oil and gas industry where they play a major role in the ongoing minimisation of risks," says Dr. Bissel, Vice President Sales Europe/Africa from the steel pipe manufacturers Vallourec. Industrial safety and environmental protection have always been central issues in the oil and gas industry and are therefore also crucial priorities for suppliers, including the steel pipe industry. "All stakeholders need to have an assurance of the highest possible safety. Even under today's cost pressure," says Bissel, "the industry mustn't lose sight of a vital priority: 'safety everywhere and at all times'." For environmental reasons Vallourec now also offers pipe connections that can do completely without lubricants (Cleanwell).
Competition from fracking
Intense pressure can be felt by the oil and gas industry not just deep down below sea level, in their pipelines. But the demand situation, too, has developed far less positively than expected. "Following the Arab Spring and thus high expectations in the Middle East, a large number of projects were initiated which subsequently caused overcapacities," says Dr. Dirk Bissel. At the same time, the increase in productivity and therefore competitiveness of US shale gas was clearly underestimated.
So-called fracking – extracting oil and gas from shale stone – is very much in competition with traditional oil production at the moment and is increasing the volume of oil that is traded throughout the world, says Markus Zimmermann from Schoeller Werk. Any decisions by OPEC to stabilise oil prices and to reduce the production volume are therefore having relatively little impact.
More orders expected in 2018 again
The offshore industry has been highly volatile over the last few years. "The sharp drop in oil prices has led to a decline in sales here recently," says Dr. Zimmermann, "resulting in fewer orders from energy companies." But there may well be a trend reversal soon. "We reckon there’ll be some slight recovery over the next few years, so that – like other suppliers to the offshore industry – we're likely to receive more orders again in 2018."
There has also been considerable pressure on the Norwegian oil industry. Norway is particularly well known for its big oil and gas industry, which contributes around 20 per cent to the country's annual economic output. Norway is now having to secure its position on the oil market for the next 30 years.
Production due to start in late 2019
All the relevant conditions are in place, as there are enormous oil and gas reserves just off the Norwegian coast. One of them is the Johan Sverdrup Oil Field, one of Norway's biggest oil fields, with an overall volume estimated between 1.7 and 3.0 billion barrels. The deposit is situated 120 metres (400 feet) below sea level and is 1,900 metres (2,600 feet) deep. The entire area covers around 200 square kilometres (77 square miles).
About 12 billion euros is being invested in the first stage of development. This includes the drilling holes, installing feed pipes and particularly also setting up four fixed platforms. “These are a processing platform, a riser platform, a drilling platform and a living quarters platform, all connected by bridges with lengths between 80 and 100 metres (60 and 330 feet). Two further platforms will be added at the next stages. Once production has started at the end of 2019, Norway is expecting to extract oil from this field until 2050. Day by day, a pipeline will then take some 550,000 barrels to the Mongstad Terminal in Hordaland.
Over 1,400 tonnes of total weight
Butting received a contract for the production of longitudinally welded pipes for all four platforms and also for the connecting bridges. "The requirements on materials at sea are very high due to the enormous stress caused by the salty air. Butting therefore used 6 Moly, 316L, Duplex and Superduplex as materials," says Christian Schenk from Sales CRA Pipes. The dimensions of the pipes, made and delivered by Butting, range from OD 2” to 30” with lengths of 6 to 12 metres (20 to 40 feet). The pipes supplied to the Johan Sverdrup Oil Field had a weight of over 1,400 tonnes in all.
The transportation of energy is a major focal area in nearly all of Europe, e.g. the Trans-Adriatic Pipeline (TAP) which forms part of the Southern Gas Corridor, due to take gas from Azerbaijan to western and south-eastern Europe from 2020 onwards. It connects with the Trans-Anatolian Pipeline (TANAP), runs through Greece, Albania and the Adriatic Sea, and eventually reaches Italy, covering around 870 kilometres (540 miles) in all.
Engineering Supports und Trainings
Almost one third of the TAP pipeline was supplied by the Salzgitter group via its international trading organisations. This included 270 kilometres of large-diameter pipes of the EUROPIPE joint venture and 1,559 pipe bends supplied by the pipe bending plant in Mülheim with a total tonnage of some 170,000 tons for the onshore area in Albania. More than 71,000 tons of large-diameter pipes are scheduled for the 105 kilometres long offshore part of this pipeline along the Albanian coast to Italy. A top order at its best.
What are today's expectations on suppliers to the oil and gas industry? According to Vallourec, there is currently an increasing demand for pipe-related services, especially technical consultancy and application-focused training, ranging from lectures for drilling engineers to training sessions for entire rig crews. Lifetime management, too, is gaining in importance. The aim is "to provide highly efficient technical systems that will give each customer maximum support in reaching their cost optimisation target. The customer looks at the entire cost of a given investment, including running expenses and also any repairs and servicing that may be required. It's the total cost of ownership that matters," says Dr. Dirk Bissel from Vallourec.
Service along the entire lifecycle
Comprehensive solutions are expected in all the product segments of a seamless pipe manufacturer – OCTG, line pipes, drill pipes and Serimax welding services – covering the full range, from simple tasks to high-end solutions for complex operations in oil and gas fields.
Such services often accompany the entire lifecycle of a product and project. Technical support starts at a very early stage, "so that the customer can receive support and advice in choosing the most efficient technology," says Bissel. As pipe manufacturers, Vallourec, for example, provides a system called Cleverscan for optimising the welding of pipe ends. This service goes far beyond the production of seamless pipes.
More realistic demand forecasts
But even though there are positive indications in the development of the oil and gas industry and therefore also positive effects on the steel pipe industry in 2018, Dr. Dirk Bissel from Vallourec can see "uncertainties in the demand forecast". They depend on developments of business activities in the BRIC states, though also in Europe and America. The demand is apparently there, and new projects are being launched throughout the world.
Nevertheless, "projects will be scrutinised more critically for their economic viability, and positive decisions will be based on far more realistic demand forecasts and price developments," sums up Bissel. Although, in the medium term, a boom in demand is unlikely, “the market situation will stabilise at a healthy level," as oil and gas will continue to be an indispensable source of energy for a very long time.
Questions for the future
However, there are questions about the future. "We, too, would like to know what the future relationship will be between fossil fuel and renewable energies," says Markus Zimmermann, head of Energy Sales at Schoeller Werk. Decisive factors will include new developments and political decisions.
Yet alongside traditional oil and gas production, we will also see new business segments opening up. What Vallourec finds particularly interesting for Europe is solutions in the geothermal sector – another industry with some good depth and good future prospects. The oil and gas industry will continue to demonstrate its ability to handle pressure.
Source: Tube